In the modern world, metal and electricity are two of the most common combination of elements we encounter in our daily lives. At the same time, we see a natural process still in play even in this rapidly advancing era, especially on the electrical equipments, be it as common as household appliances or the large electrical machineries we see in manufacturing plants. The natural process we are talking about is corrosion. The effect of corrosion is so drastic that corroded equipment can cause electrical system downtime and failure that are not only is very costly, but will increase risk of accidents and even injuries.
What is corrosion?
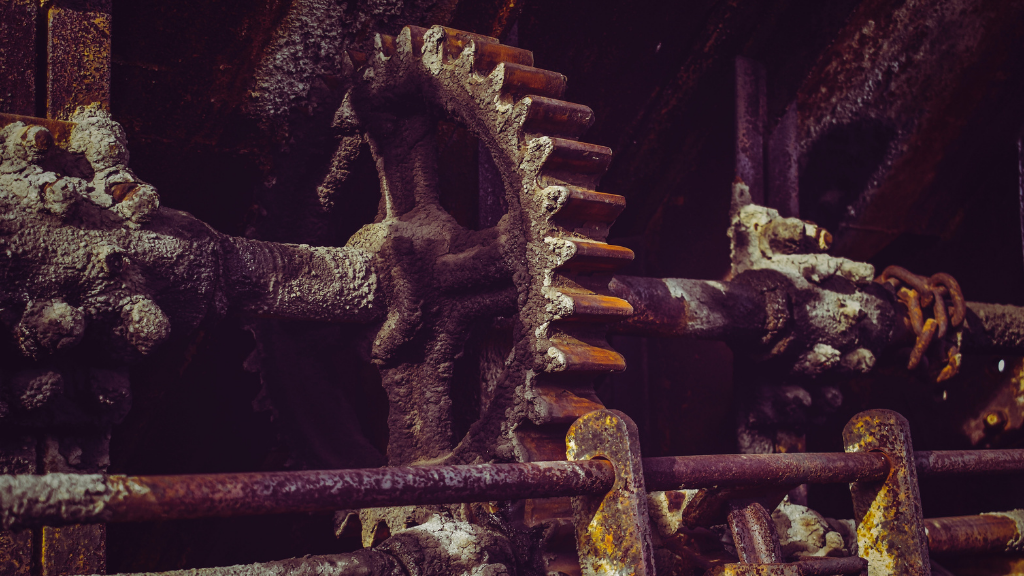
Corrosion is a deterioration that usually happens to metal and what we commonly called rust. This process gradually destroy the metal through the chemical or electrochemical reaction with the environments. While corrosion can happen on various metals, the combination of metal and electric in an electrical equipment is more prone to corrosion. This is due to the electrochemical reactions, and an increase in the electrical conductivity of the electrolyte that will speed up the corrosion process. Because its natural, corrosion is an inevitable process that cannot be avoided but there are preventive and controlled measures to reduce occurrences of the process. To understand how corrosion can be prevented, we must first understand the environments that can cause corrosion.
Corrosive Environments
- Corrosive Environments
- The quantity of sodium chloride or salt can be found in the seawater and can travel through coastal winds, mist, fog, and sea-spray that can go up to 8km from the shore.
- Industrial Corrosion
- Air contaminants are common in highly industrial environment. Toxic emissions from factory vehicles and industrial dusts which can be extremely corrosive when exposed to oxygen, water or humidity.
- Rural Locations or Farms
- Farming equipment are highly susceptible to corrosion due to its usage in the Farm. Some of the most corrosive chemicals can be found in fertilisers. Animal waste and diesel fuel can also contribute to rapid corrosion.
Corroless® CCI For Preventive Measures

Corroless Corrosion Inhibitors technology creates a way to continuously releasing a vapour with powerful anticorrosion properties. With the protective vapour coating, the metal surface is conditioned to exclude oxygen and moisture to completely stop the process of corrosion. The application of the vapour forms a monomolecular film on the surface of the metal to create ionically insulating barrier between the substrate and the environment. The vapour also effectively covers all recessed areas and cavities to give full protection of the metal.
The Corroless® range of corrosion control coatings and vapour phase corrosion inhibitors are known to effectively protect both ferrous and non-ferrous metals and can be used to prevent dissimilar metal corrosion. Corroless technology has been implemented into powder, oils, greases, waxes and water-based products that can be easily used on almost all applications. The fine components of the Corroless corrosion inhibitors allow the coating to reach even the unreachable or hidden parts in the electrical equipment, complex and inaccessible equipment, where it would be impractical to use a conventional coating, without impairing the conductivity or magnetic properties. The coated parts also do not react with plastic or rubber that are common components in an electrical equipment as well.
The main benefits of Corroless CCI are:
- Excellent chemical and corrosion resistance
- Long and extended protection
- Competitive costs
- Long-term cost savings
- EASY to apply, SIMPLE to remove.
- FAST re-commissioning.
Corroless products are ideal for the management, preservation and rehabilitation of electrical equipment that are exposed to various kinds of environments with extreme wear and tear. With the right consultation, maintenance of any electrical equipment and machineries can be optimised against corrosion. For more information, consult us at ask@ats-grp.com.